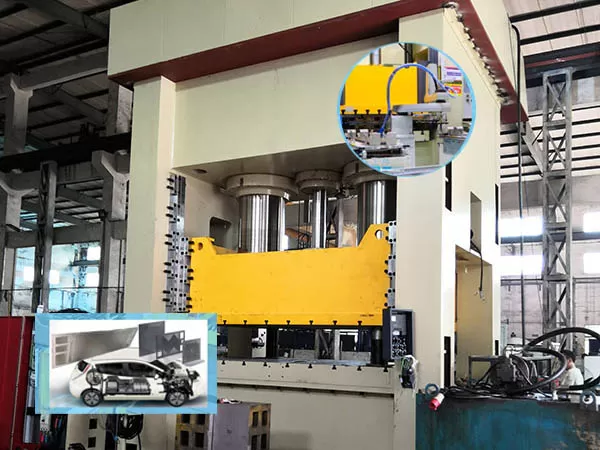
Hydraulic Presses for Automotive Manufacturing:10 Innovative Applications
1. Battery module press:
During the assembly process of new energy vehicle battery modules, hydraulic press equipment relies on high-precision pressure control and stable output to press the battery cells together evenly and tightly, ensuring good contact and electrical connection between batteries, avoiding battery damage or poor contact caused by uneven pressure, and improving the consistency and reliability of battery modules.
2. Battery shell forming:
Hydraulic forming technology processes metal sheets or other materials into battery shells that meet design requirements by precisely controlling hydraulic pressure and mold movement. The three-beam six-column structure and other designs of the hydraulic press give it good rigidity and stability, ensuring high precision during the shell forming process and providing reliable physical protection for the battery.
3. Battery pack sealing and testing:
Hydraulic technology can be used to drive sealing test equipment to detect leakage and other problems by applying a certain pressure to the battery pack. At the same time, during the sealing process of the battery pack, hydraulic equipment can also accurately control the amount and pressure of sealant to ensure the sealing effect and improve the safety and service life of the battery pack.
4. Metal stamping and forming:
Servo hydraulic presses use the combination of hydraulic technology and servo control technology to achieve precise stamping of metal sheets and forming of complex shapes. It can quickly and accurately stamp metal sheets into parts of various shapes, such as doors, hoods, body side panels, etc., according to the requirements of the body design, meeting the high precision and high quality requirements of automobiles for body structural parts.
5. Internal high pressure forming:
Internal high pressure forming is an advanced hydraulic forming technology. By applying high pressure liquid inside the tube, the tube expands in the mold and fits the mold shape, thereby forming complex hollow structural parts, such as torsion beams, left and right longitudinal arms, automobile exhaust pipes and other lightweight chassis parts for automobiles. This process can not only reduce the weight of parts and improve the energy efficiency of automobiles, but also enhance the strength and rigidity of the car body and improve the safety performance of the car.
6. Thermoforming process assistance:
In the thermoforming process of automobile bodies, the hydraulic system can provide stable pressure and flow for the cooling device to ensure the uniformity and stability of the cooling process, thereby improving the quality and performance of thermoformed parts.
7. Chassis component forming:
The chassis of the automobile involves a large number of complex curved surfaces and precision structural parts, such as frame longitudinal beams, suspension brackets, subframes, steering knuckles, etc., which require extremely high forming accuracy. The high-precision synchronous control system equipped with the four-column hydraulic press can control the synchronization error within a very small range through the coordinated operation of multiple hydraulic cylinders, ensuring that the chassis components are evenly stressed during multi-process forming such as stretching, bending, and punching, avoiding structural deformation or dimensional deviation caused by uneven pressure.
8. Automotive interior molding:
The automotive interior hydraulic press uses hydraulic technology to realize the molding and processing of interior parts. It presses molds of various shapes on plastic materials through the push of hydraulic cylinders to form them. Compared with traditional processes, it has the advantages of stable quality, high efficiency and energy saving, and high degree of automation. It can be used in the processing of interior parts such as roof interiors, seat pads, door panels, and center consoles.
9. Composite material component production:
With the trend of lightweight automobiles, the application of composite materials is becoming more and more extensive. The hydraulic press can accurately control pressure and temperature to ensure the molding accuracy and quality of composite material components, helping automakers to effectively reduce the weight of the car body and improve fuel efficiency. For example, it is used in the compression molding of large carbon fiber body panels, fiberglass fan blades, etc. Its uniform pressure distribution characteristics can avoid composite material stratification and improve the strength of the product.
10. Engine parts processing:
Hydraulic presses can be used to produce core parts such as engine cylinders, pistons, and connecting rods, and improve material density and mechanical properties through high-pressure forming processes. For example, in the forging of automobile piston rods, hydraulic presses can ensure the uniformity of metal structure and meet high strength requirements.
Hydraulic presses are widely used in automotive manufacturing for a variety of tasks, including stamping, forming, and assembly. They are essential for creating body panels, frames, and other critical components with high precision and minimal waste. Hydraulic presses offer benefits like precise pressure control, consistent production quality, and energy-saving options.