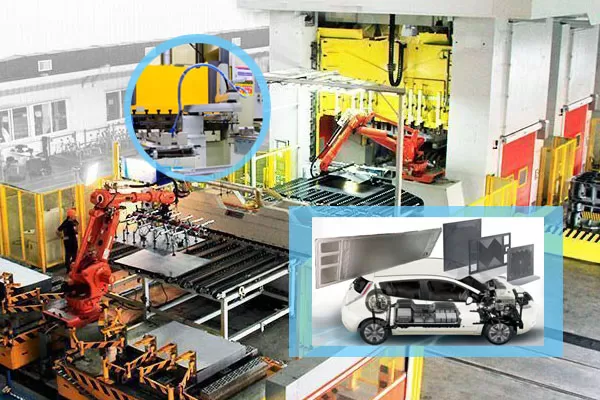
Key Features of the Fully Automated System
1. Hydraulic Pressing Unit
● High-tonnage hydraulic press (100–1000 tons, depending on plate size)
● Precision-controlled pressure & stroke (servo-hydraulic or CNC-controlled)
● Multi-stage pressing (pre-forming, embossing, final compression)
● Quick die-change system (for flexible production)
2. Automated Material Handling
● Robotic loading/unloading (6-axis robots or gantry systems)
● Automatic lead strip feeding (uncoiler, straightener, feeder)
● Conveyor belt systems for plate transfer between stations
● Scrap collection & recycling (minimizes material waste)
3. Smart Control & Monitoring
● PLC + HMI (Siemens, Allen-Bradley, or Mitsubishi-based control)
● IoT-enabled sensors (pressure, temperature, position feedback)
● Real-time production tracking (OEE monitoring, defect detection)
● Predictive maintenance alerts (vibration, hydraulic fluid quality)
4. In-Line Quality Inspection
● Laser micrometers (thickness & flatness measurement)
● Vision inspection systems (detects cracks, deformations)
● Automated weight check (ensures consistency)
● Defective plate rejection (automated sorting)
5. Post-Processing & Packaging
● Automatic stacking & palletizing (robotic or pneumatic)
● Batch counting & labeling (RFID/barcode tracking)
● Packaging automation (shrink-wrapping, boxing)
Production Workflow
1. Material Feeding
● Lead alloy strips are fed automatically from a coil.
● Straightening and cutting to required dimensions.
2. Hydraulic Pressing
● Pre-forming to create the grid structure.
● High-pressure embossing for active material adhesion.
● Final pressing for dimensional accuracy.
3. Trimming & Flash Removal
● Excess material is trimmed off.
● Deburring for smooth edges.
4. Automated Quality Control
Vision inspection for defects.
Weight and thickness verification.
5. Stacking & Packaging
● Plates are stacked in batches.
● Automated packaging for shipment.
Advantages of Full Automation
● Higher Productivity – 24/7 operation with minimal downtime.
● Consistent Quality – Eliminates human errors in pressing & handling.
● Lower Labor Costs – Requires only 1-2 operators for monitoring.
● Flexible Production – Quick changeover for different plate designs.
● Improved Safety – Reduces worker exposure to lead dust & heavy machinery.
● Data-Driven Optimization – Real-time analytics for process improvement.
Goodsjack/Delishi specializing in custom hydraulic press and production line acoording to customers' requirements. Please contact us for your own hydraulic press solution.