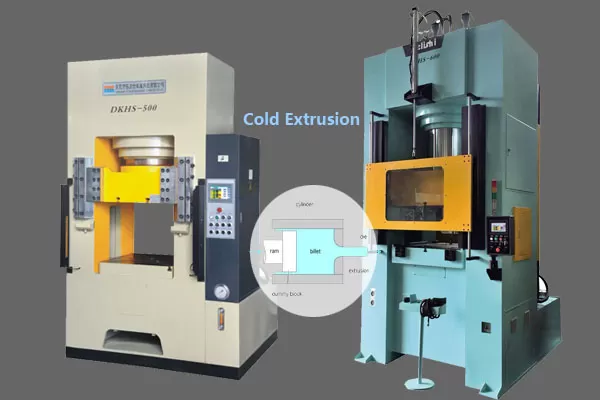
1. Pressure Stability
Pressure stability refers to the hydraulic system's ability to maintain consistent pressure during the extrusion process, minimizing fluctuations that could affect part quality.
Key Aspects:
● Hydraulic System Design:
○ High-quality pumps, accumulators, and servo valves ensure stable pressure output.
○ Closed-loop pressure control systems adjust in real-time to maintain consistency.
● Pressure Fluctuation Tolerance:
○ Premium presses maintain pressure variations within ±1% to ±2% of the set value.
○ Excessive fluctuations lead to defects like incomplete filling or cracking.
● Load Compensation:
○ Advanced systems compensate for load changes during forming to prevent pressure drops.
● Impact on Extrusion Quality:
✔ Consistent material flow → Uniform part density & mechanical properties.
❌ Unstable pressure → Defects (e.g., voids, cracks, dimensional inaccuracies).
2. Forming Accuracy
Forming accuracy measures how closely the extruded part matches the intended design dimensions and geometry.
● Key Influencing Factors
○ Machine Rigidity & Frame Design:
High-stiffness frames (e.g., four-column or pre-stressed frame designs) reduce elastic deformation under load.
● Precision Guidance Systems:
○ Linear guides or precision bushings ensure smooth, repeatable ram movement.
● Die & Tooling Quality:
○ Hardened, precision-ground dies minimize wear and maintain tolerances.
● Control System Precision:
○ CNC-controlled presses offer better accuracy (±0.01–0.05mm) than conventional hydraulic presses.
● Common Accuracy Metrics:
✔ Dimensional Tolerance: Typically ±0.05–0.1mm for high-precision cold extrusion.
✔ Surface Finish: Smooth extrusion (Ra 0.8–3.2 µm) reduces post-processing needs.
❌ Poor accuracy → Increased scrap rates & secondary machining costs.
Optimization Strategies for Better Performance
1. Use Servo-Hydraulic Systems – For precise pressure & speed control.
2. Real-Time Monitoring & Feedback – Sensors adjust parameters dynamically.
3. Regular Maintenance – Check seals, hydraulic fluid, and tool alignment.
4. Advanced Simulation – Finite Element Analysis (FEA) predicts material flow & optimizes die design.
Conclusion
For hydraulic cold extrusion presses, pressure stability ensures defect-free forming, while forming accuracy guarantees dimensional precision. Investing in high-end hydraulic controls, rigid frames, and precision tooling maximizes performance in demanding applications like automotive, aerospace, and fastener manufacturing.