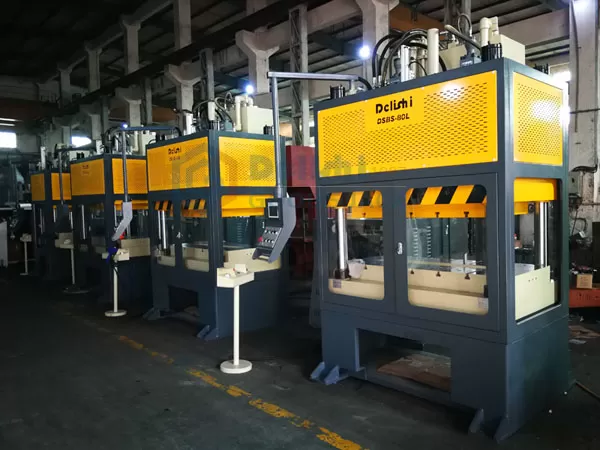
Six major advantages of energy-saving transformation of hydraulic press machines
High energy saving
Compared with traditional quantitative pump and variable pump systems, the servo system adopts double closed-loop control of pressure and flow, and the energy saving rate can reach 20%-80%. Compared with the vector frequency conversion system (self-proclaimed asynchronous servo system), the energy saving is more than 20%. The servo system uses a permanent magnet synchronous servo motor. The efficiency of the motor itself is as high as 95%, while the efficiency of the asynchronous motor is only about 75%.
High efficiency
The servo response speed is fast, and the pressure rise time and flow rate rise time are as fast as 20ms, which is nearly 50 times faster than asynchronous motor. It improves the response speed of the hydraulic system, reduces the action conversion time, and speeds up the operation speed of the entire machine. It adopts variable phase field weakening control technology to increase the motor speed to a maximum of 2500RPM and increase the output of the oil pump, thus increasing the speed of mold opening and closing.
High precision
The fast response speed ensures the accuracy of mold opening and closing, and the closed-loop speed control ensures the high repeatability of the ejection platform position, and the products produced are accurate and consistent; it overcomes the changes in the grid voltage, frequency, etc. of the ordinary asynchronous motor quantitative pump system. The changes in rotation speed caused by the change in flow rate will lead to the disadvantage of lowering the product yield.
Safe and stable
High reliability retains the original control method of the hydraulic press; prompts alarm when a fault is found, and has multiple protections such as overvoltage, overcurrent, overload, overheating, undervoltage and short circuit to ground. The products have excellent manufacturing technology and can adapt to harsh industrial environments.
Lower oil temperature
The injection molding machine oil circuit system that adopts the servo hydraulic drive control system significantly reduces its own heat, keeping the oil temperature at a lower temperature, significantly extending the service life of the hydraulic system components and hydraulic oil, and reducing the hydraulic system failure rate. The system oil temperature is greatly reduced, and cooling water can be saved by about 30-60%.
Reduce consumption
Reduce noise: Using servo hydraulic drive control system, the noise is significantly reduced, improving the working environment and making it more environmentally friendly. Equipment protection: Reduce the impact of mold opening and clamping, and extend the service life of mechanical equipment and molds.
Hydraulic press servo energy saving investment return
Take 5 sets hydraulic press machines as an example: the total power is 275KW, they work 26 days a month, 22 hours a day, the load rate is 40%, the power saving rate is about 40-60%, and the calculation is based on the 45% power saving rate. Average monthly electricity consumption: 275kw*26*22*40%=62920 kilowatt-hours. Monthly electricity cost savings: 62920*45%*0.85=24066.9 CNY. Annual electricity cost savings: 24066.9*12=288802.8 CNY. The normal investment recovery cycle is 12-18 months